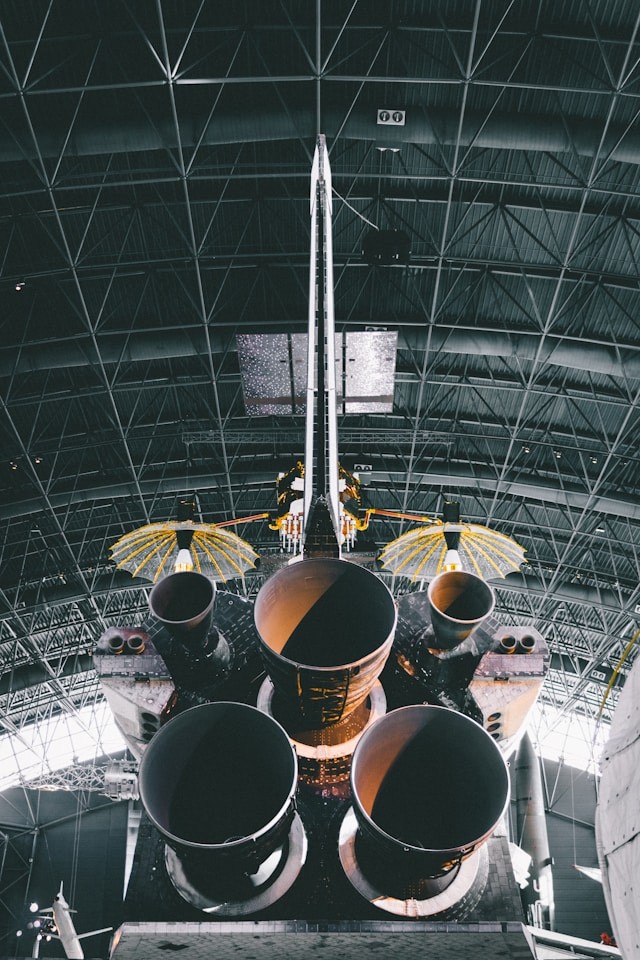
Relativity Space, a company using 3D printing to build its launch vehicles, has secured an $8.7 million contract with the US Air Force Research Laboratory (AFRL) for real-time flaw detection exploration in additive manufacturing.
The Ribbon-Cutting of A New Additive Facility
The Air Force Research Laboratory (AFRL) held a ribbon-cutting ceremony on November 9, 2022, marking the reopening of its renovated Additive Manufacturing Laboratory and installing a new 3D printing system for aerospace-grade materials.
RX, AFRL's Materials and Manufacturing Directorate organized a tour of its Computed Tomography Laboratory to highlight recent infrastructure upgrades and the introduction of a new Computed Tomography machine and suite. These machines are capable of non-destructive testing, allowing for the detection and measurement of internal geometry, defects, manufacturing errors, and failure modes in materials produced by additive manufacturing.
AFRL allocated approximately $6 million in Flex-4 funding to finance the renovations. Flex-4 funds from the Department of Defense facilitate unique capabilities in research labs. Upgrading the two lab spaces and adding new machines will help AFRL cut costs, speed up research, enhance worker safety, boost efficiency, and maintain material integrity.
In the past, replacing aging aerospace parts has been costly and challenging. Still, if material quality can be ensured, additive manufacturing can save time and money by meeting the demand for replacement parts.
Relativity Space's Real-Time Flaw Detection
Real-time flaw detection in 3D printing involves spotting defects as parts are being printed. This is crucial because additive manufacturing builds objects by stacking thin layers of material, increasing the chances of imperfections with each layer.
AFRL's Materials and Manufacturing Directorate at Wright-Patterson Air Force Base, Ohio, provided the two-year research contract, which will take place at Relativity's factory in Long Beach, California, utilizing the company's Stargate 3D printing platform, renowned for its ability to print large-scale metal objects. Adam Hicks, a physicist at AFRL's Materials and Manufacturing Directorate, mentioned to SpaceNews that the collaboration with Relativity Space is a response to a congressional demand signal.
A Legislative Mandate
In the National Defense Authorization Act, Congress directed the Defense Department to examine how additive manufacturing could speed up the production of aerospace components and vehicles. Lawmakers also required the DoD to create a network of domestic suppliers to assess these technologies.
Hicks mentioned that AFRL will collaborate with Relativity on real-time flaw detection in large-format additive manufacturing to investigate different in-situ process monitoring and post-build non-destructive evaluation techniques, as well as advanced robotics, automation, and digital enterprise tools.
Nondestructive evaluation techniques check the quality and integrity of the final product by inspecting the structure of a part without causing damage. Relativity Space will create and validate a real-time flaw detection system to identify, locate, and categorize defects as printing occurs. Data will be consolidated to establish a complete digital thread.
Aerospace's Digital Thread
A digital thread serves as the central nervous system for the entire lifecycle of a platform like an aircraft, spanning from design through disposal. According to aerospace engineering, it is formed by data that connects different stages of the aircraft's existence.
Relativity Space is among the pioneering companies utilizing additive manufacturing in aerospace, which offers benefits such as shorter lead times, greater design flexibility, and lighter parts.